BLOG
Industrial Connectivity: How the Internet of Things Empowers Manufacturers
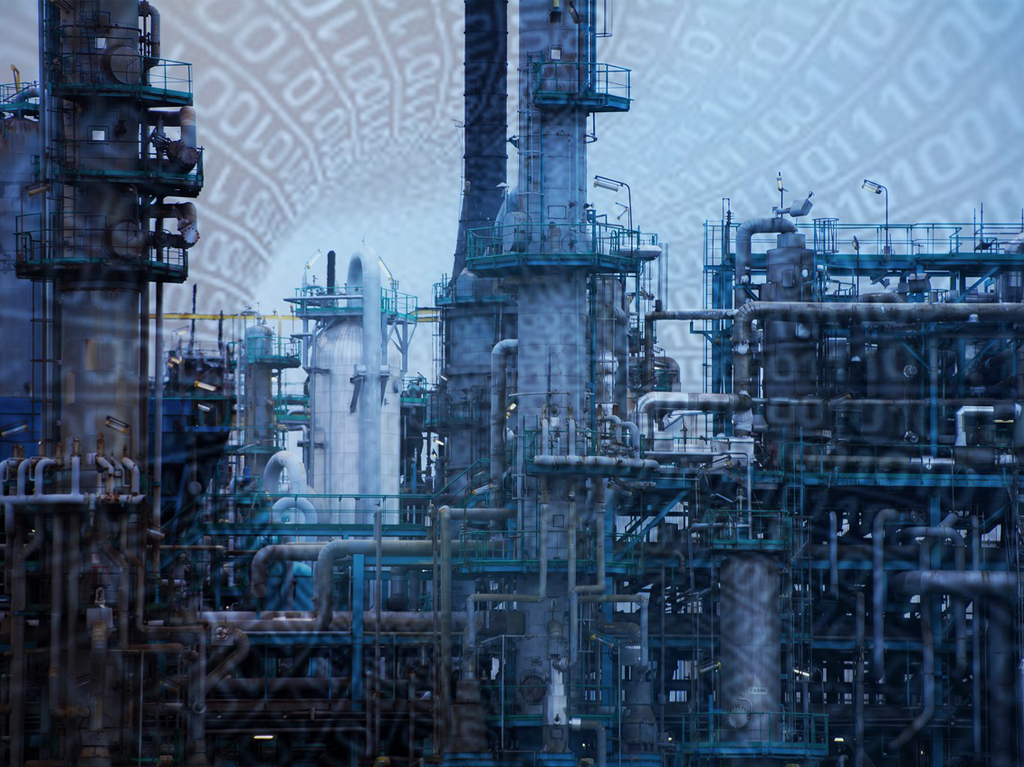
Internet of Things (IoT) technology has continued to impact every industry in massive ways, and the manufacturing industry hasn’t been left behind. The information technology (IT), medical products, consumer products, and the automotive industry are all leveraging IoT and related technologies to streamline their processes and improve efficiency.
Typically, IoT creates a connected world from the “edge” (actuators, sensors, and controls) using computer applications (on-site computing, embedded systems, and cloud computing) to enhance efficiency and productivity in a myriad of use cases. IoT edge devices interlink multiple uniquely identifiable electronic devices through the Internet “data plumbing,” such as Web Services, Internet Protocol (IP), and Cloud Computing.
Promising IoT Use Cases in Manufacturing
Although the manufacturing industry is one of the last adopters of IoT technology, there are several promising use cases. Here are some ways the internet of things is empowering manufacturers:
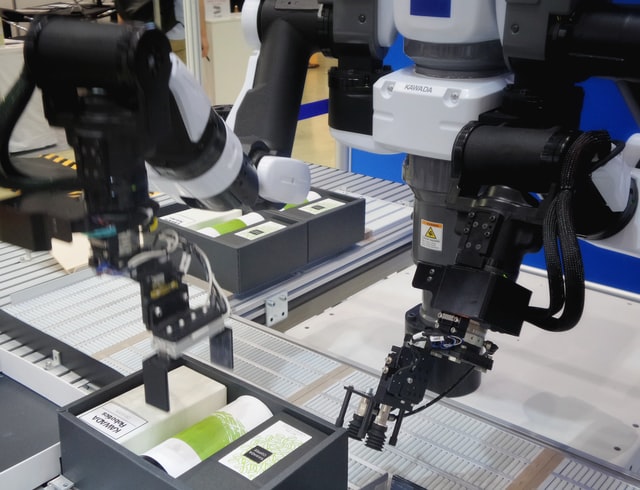
1: Digital Factories
The Internet of Things helps establish a connection between your manufacturing facility and the manufacturers of the equipment you use for production, supply chain managers, and employees involved in product design. Having a connected factory makes it easier and cost-effective to maintain and manage manufacturing processes.
The digital connection between various areas of your plant allows managers to track employee performance, feedback from end-users, and the efficiency of equipment installed. IoT also makes it seamless and 100% paperless to share crucial data between team members.
2: Quality Control
IoT can help you control product development at every stage by tracking the quality of materials, the quantity of waste created per product, the temperature of the manufacturing environment, and so on. The plant manager can get detailed reports of every step of product design, transportation of raw materials, and distribution of finished goods. As a result, manufacturers can implement in-depth quality controls, improve workflow, secure manufacturing environments, and enhance the quality and efficiency of equipment and vehicles used for transportation.
3: Supply Chain Optimization
IoT-enabled devices can help manufacturing companies track products funnelled through the supply chain. In addition, you can integrate these devices into PLM, ERP, or other systems your company uses for data storage and reporting. In case your supply chain deviates from the plan, IoT will help you trace back to the root cause of the delay since all the interdependencies are tracked.
4: Packaging Optimization
Internet of Things can help collect usage patterns and reports on how customers use your product in real life. As a result, production managers can rework the packaging, change the design, and reduce costs to resonate with the end consumer on a deeper level.
5: Facility Management
Smart manufacturing devices and IoT can improve the speed and quality of your facility maintenance. Managers often have to oversee temperature-sensitive or vibration-sensitive equipment or devices impacted by the slightest environmental changes.
Without the help of advanced technology such as IoT, predicting deviations from optimal functionality parameters can be practically impossible. IoT sensors can alert the facility manager instantaneously whenever there are changes that could jeopardize manufacturing tools. By controlling your manufacturing environment with IoT-powered facility management solutions, you can reduce maintenance costs, minimize downtime, and enhance operational efficiency.
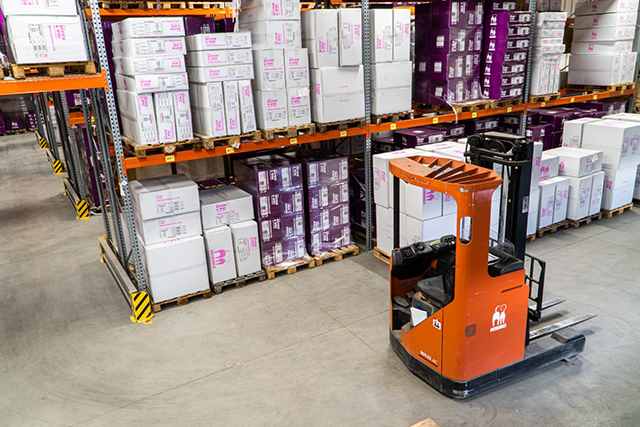
6: Inventory Management
Through the IoT, factory managers can trace all the raw materials required for manufacturing on the item level. As a result, you can seamlessly renew the inventory without putting the production process on hold. Additionally, you can improve inventory planning once you implement the Internet of Things. You’ll be able to predict how much time it would take for a certain quantity of resources to run out. IoT can also increase the precision of long-term production planning.
7: Plant Security Management
Besides enhanced production efficiency, IoT manufacturing also impacts workplace safety and the security of the manufacturing site itself. Wearable health trackers can alert managers as soon as an employee develops an injury risk or health issue.
Additionally, you can use IoT to keep track of the overall number of on-site injuries and health-related incidents in the manufacturing process. With that insight, you can find out the root cause of such situations and devise ways to predict and mitigate similar incidents in the future.
IoT can also be useful for theft protection as it can notify facility managers in case of equipment and property damage. It helps keep logs of the time when a specific machine was broken, stolen, or lost.
8: Condition-Based Downtime Alerts
Traditional plant maintenance is often laborious and time-consuming. It may also fail to provide manufacturers with clear insights into plant performance and the inhibitors of the production flow. Random factory inspections, walk-throughs, and annual shutdowns often provide a selective understanding of the manufacturing process and not the bigger picture.
Fortunately, the Internet of Things helps manufacturers implement a proactive site management approach, a condition-based management system. By obtaining IoT-based downtime alerts, you can improve throughput and minimize machine downtime.
9: Remote Equipment Management
Connected sensors allow production managers to oversee the state of factory equipment without having to visit the site physically. As a result, it improves employee productivity, creates proper storage conditions for tools and equipment, and reduces production costs.
10: Real-time Production Monitoring
Last but not least, the Internet of Things allows all stakeholders involved in the manufacturing process to get real-time updates on the production flow. This improves the speed and efficiency of communication and enhances the overall manufacturing pace. With real-time monitoring, your organization can reduce the amount of work performed during regular production cycles and eliminate waste.
Wrapping Up
Overall, the manufacturing industry is the most equipped to showcase the full potential of IoT. Manufacturers can use IoT sensors to restructure their old-fashioned processes from scratch, manage supply chains, monitor equipment quality, improve employee productivity, and predict potential issues long before they arise.
As with all connectivity related tech, Allo Technology is here to ensure your area gets the service it needs to . Our backbone network runs on the latest Dense Wavelength Division Multiplexing (DWDM) technology which provides better network resiliency and higher bandwidth capacity to support the transmission of high capacity of data, bringing to you the future of high speed connectivity and associated benefits. The future is looking bright for industrial connectivity, and we’ll be walking with you every step of the way. Contact us today to schedule your free no-obligation consultation!